Case Study
S-BMP-OHS-2013-001-01
Russell Jordan is fairly new to the cane industry. After spending 14 years under car bonnets as a mechanic, Russell was determined to try life on the land, and in 2001 bought a 120 hectare farm in the Burdekin region.
Russell and his wife Susie own and operate their cane farming business near Giru. In recent years he experienced inadequacies in the management of various contractors he engaged to assist with his farm operations. After working with workplace health and safety plans in his previous career as a mechanic, Russell saw an opportunity to improve safety practices and plans on his cane farm.
In 2010, Russell Jordan introduced a contractor management program to his cane farming operations. The program was designed to be integrated with his CANEGROWERS Health and Safety Management System, “Ten Steps to Safety”.
In the past, many business outcomes were discussed and sealed with a handshake. Russell identified this as a shortfall in his obligations to maintain a safe work environment. A more formal process to engage contractors was needed. The Jordans decided on a documented procedure that would require a ‘safe work contract’ which highlighted the responsibilities of all parties in the contract.
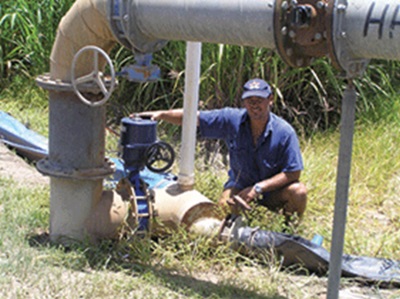
Russell Jordan on farm near Giru, in the Burdekin region.
Contractors are also required to submit a safety plan for their operations that contained emergency response planning and proof of a current workers compensation insurance policy and when needed proof of delivery point induction training for all cane haulage workers. Russell also encouraged consultation with contractors and their workers by discussing known hazards as well as showing their key locations with a simple property drive through inspection.
“After the induction, the contractor, all of his drivers and I sign the document,” he said. Russell commented that even though he had a safety management system, it was a living document and needed to be supplemented with new ideas and reviews of the processes already in place.
Since buying two more farms in the region, Russell has developed safety plans for each of these separate properties as each farm is different, and has compiled them all into one handbook. “It took a little effort to set up initially, but now each year I just review each farm’s safety document and make small adjustments if necessary,” he said.